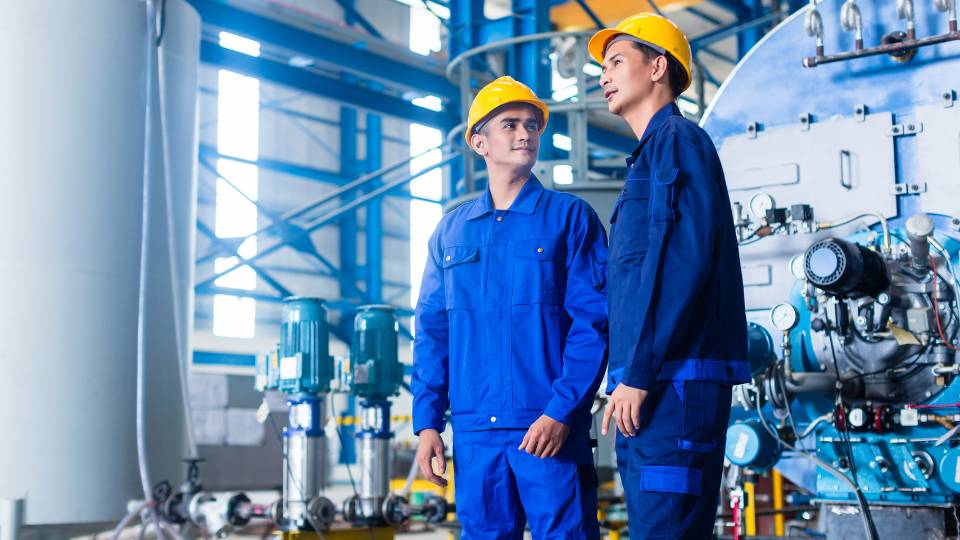
Manufacturing is a powerful engine for our economy, but how can we ensure it runs efficiently and reduces manufacturing waste? Let’s explore ten key questions that manufacturers should consider when implementing sustainable waste management practices.
What waste are we generating?
Understanding the types of waste produced by your facility is the foundation for any sustainable strategy. This goes beyond simply knowing you have “scrap.” Delving deeper involves identifying the specific materials being wasted, such as metal shavings from machining or fabric trimmings in textile production. Quantifying the waste stream by type and volume helps pinpoint areas for improvement.
For instance, a furniture manufacturer might discover a significant portion of their waste comes from leftover wood scraps. This knowledge can then guide them towards exploring ways to reduce wood waste during the cutting process or finding creative uses for leftover pieces in smaller projects.
Reduce waste at the source
The most effective waste management strategy is to avoid generating waste in the first place. This might involve optimising cutting processes in metalworking to reduce scrap metal or using nesting software to ensure efficient material use in furniture production. Investing in well-maintained machinery can also reduce the production of defective products that ultimately end up as waste.
Exploring innovative design solutions like products built for disassembly or manufactured using readily recyclable materials can further contribute to waste reduction at the source. By focusing on preventing waste creation, manufacturers not only benefit the environment but also see a positive impact on their bottom line through reduced material costs.
How can we reuse or repurpose waste materials?
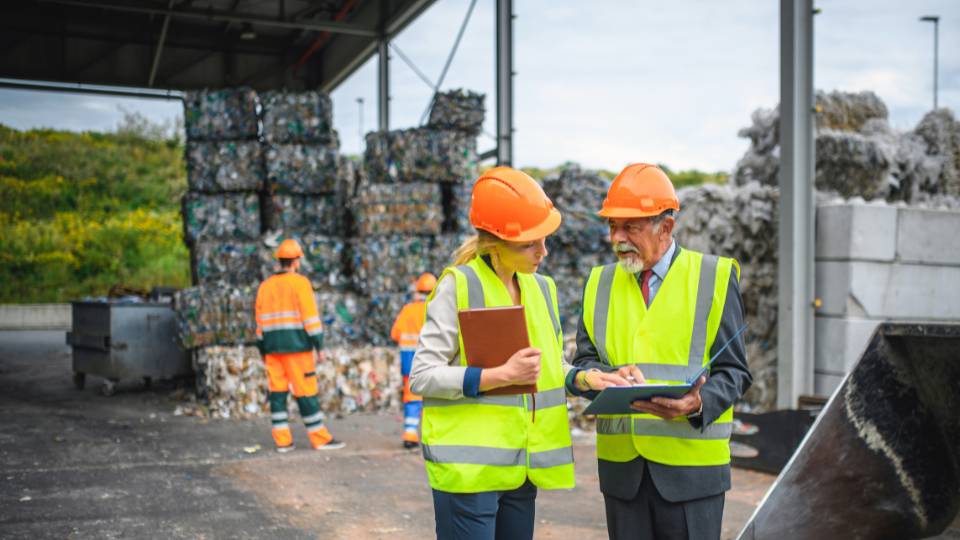
Not all waste needs to be sent for disposal. Can scrap fabric be used for cleaning cloths in a clothing factory, or leftover paint be utilising for touch-ups on products instead of being discarded? Exploring opportunities to reuse or repurpose waste materials within your own production processes reduces reliance on virgin materials and promotes a circular economy. For instance, a food processing plant might find ways to utilise vegetable scraps for composting or even develop new product lines using these “waste” materials.
Similarly, a furniture manufacturer could explore using leftover wood scraps for smaller projects like coasters or decorative items. By fostering a culture of creativity and resourcefulness, manufacturers can find innovative ways to breathe new life into waste materials, reduce their environmental footprint and potentially even discovering new revenue streams.
What are the on-site processing options for our waste?
Several techniques can help manage waste effectively on-site. Baling large volumes of cardboard or plastic reduces transportation costs and improves recycling efficiency. Investing in a baler not only streamlines waste handling but also makes it more attractive to recycling companies due to the ease of transport. Segregating different waste types at the source, such as metals, plastics, and paper, prevents contamination and simplifies recycling efforts.
Clearly labeled waste bins encourage proper sorting by employees and ensure recyclable materials maintain their value. Exploring these on-site processing options can streamline waste management, contribute to sustainability goals, and potentially even generate revenue through the sale of recyclable materials.
What are the legal requirements for storing waste on-site?
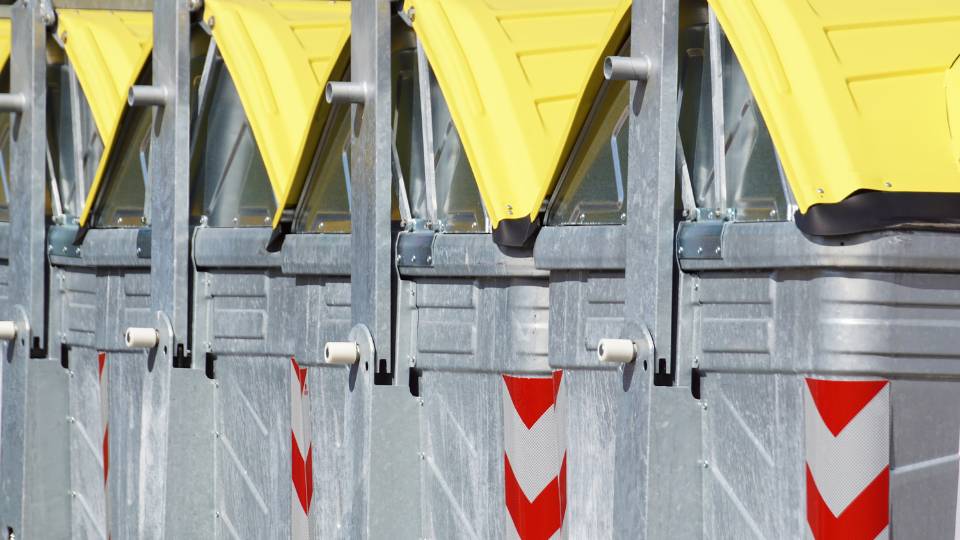
Manufacturing facilities must comply with regulations regarding waste storage to ensure environmental protection and responsible waste management. Understanding the permits and licenses required for storing specific types and volumes of waste is crucial. For example, facilities handling hazardous chemicals might need special permits for on-site storage. Additionally, proper labeling and documentation of waste streams are essential for regulatory compliance.
Waste containers must be clearly marked with the type of waste they contain, and detailed records of waste generation, storage, and disposal should be maintained. Familiarisation with local regulations and staying up-to-date on any changes ensures responsible waste storage practices that minimise environmental risks and legal complications.
How can we partner with organisations for material reuse?
Manufacturers can find valuable opportunities to reduce waste through partnerships with organisations specialising in material reuse. Material exchanges connect companies with unwanted materials to others who can utilise them in their production processes. For instance, a clothing manufacturer with excess fabric scraps could connect with a company producing cleaning cloths or craft supplies through a material exchange platform. Donation programs offer another avenue for responsible waste management.
Donating usable byproducts or excess materials to charities or educational institutions can be a sustainable alternative to disposal. Finally, collaborating with retailers or distributors to collect and remanufacture used products reduces waste and promotes product life extension. Exploring these partnerships allows manufacturers to tap into a network of organisations dedicated to material reuse, contributing to a more sustainable future.
Who regulates material reuse partnerships?
While partnerships for material reuse offer significant environmental benefits, ensuring responsible practices is essential.
Several associations play a vital role in regulating and promoting these partnerships:
- Manufacturing Industry Associations such as those found on NetRegs often develop guidelines and best practices for sustainable waste management within their specific sectors. These guidelines can help manufacturers navigate the complexities of material reuse partnerships and ensure they align with industry standards for responsible waste management.
- Recycling Industry Associations establish standards for material collection, processing, and quality control in the recycling industry. Partnering with organisations that adhere to these standards ensures the quality and integrity of the materials being reused.
- Environmental Protection Agencies set regulations for waste management and recycling, ensuring responsible practices throughout the material reuse partnerships. Staying informed about these regulations allows manufacturers to choose partners who operate within the legal framework and contribute to a sustainable waste management ecosystem.
Collaboration between manufacturers, reuse organisations, and regulatory bodies is essential for the success of sustainable material reuse programs.
How can design principles diminish waste output?
Sustainable waste management starts at the design stage. By incorporating specific design principles into product development, manufacturers can significantly reduce waste generation from the outset.
Here are some key design considerations:
- Design for Durability: Products built to last require fewer replacements, reducing waste generation over their lifecycle. For instance, designing furniture with strong joints and high-quality materials ensures its longevity and diminish the need for frequent replacements.
- Design for Disassembly: Products designed for easy disassembly facilitate repair, refurbishment, and component reuse at the end of their lifespan. This allows for valuable materials to be recovered and used in new products, extending their life cycle and diminish waste.
- Design for Recyclability: Using readily recyclable materials in product design simplifies the recycling process and increases the value of recovered materials. For example, opting for packaging made from recycled cardboard or aluminum allows for easier recycling at the end of the product’s life.
Implementing these design principles can significantly reduce waste generation in the long run and contribute to a more sustainable manufacturing process.
What role does new technology play in sustainable manufacturing?
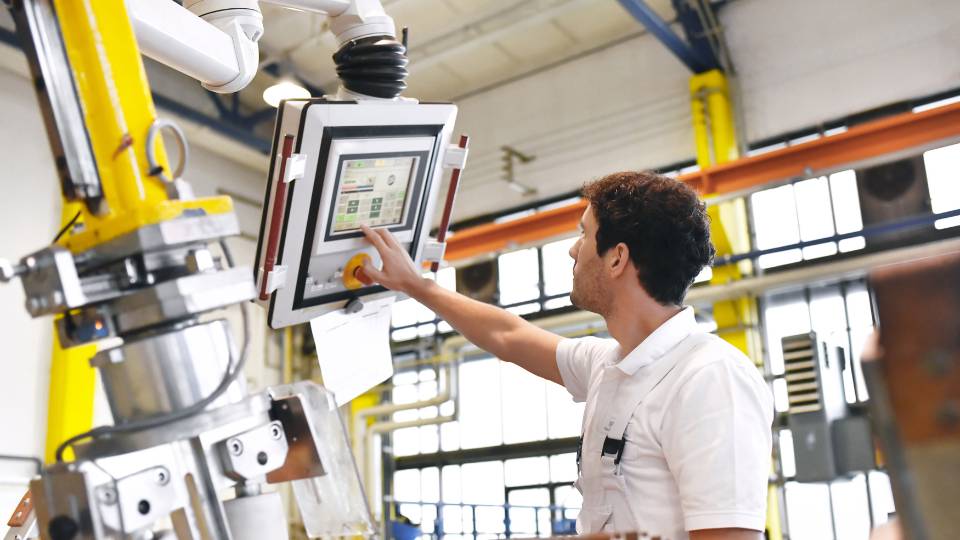
Technological advancements offer exciting possibilities for sustainable waste management. Additive Manufacturing (3D Printing) allows for precise material use, diminish waste generation compared to traditional subtractive manufacturing processes. Imagine a world where complex objects are built layer by layer, using only the exact amount of material needed. This technology holds immense potential for reducing waste in various manufacturing sectors.
Artificial Intelligence (AI) powered systems can analyse production data to identify areas for waste reduction. For example, AI can optimise cutting patterns to minimise scrap metal generation or predict equipment maintenance needs to prevent breakdowns and the production of defective products. By leveraging the power of AI, manufacturers can gain valuable insights into their waste streams and implement data-driven strategies for waste deprecation.
How can we measure the success of sustainable waste management?
Implementing sustainable waste management practices requires ongoing monitoring and evaluation. Tracking key metrics such as the volume of waste generated, the percentage of waste diverted from landfill, and the cost savings associated with waste reduction allows manufacturers to measure the success of their initiatives.
Additionally, monitoring compliance with regulations and industry standards ensures responsible waste management practices. By setting clear goals and tracking progress, manufacturers can continuously improve their waste management strategies and contribute to a more sustainable future for our planet.
Sustainable manufacturing requires asking the right questions: How can we diminish waste? What partnerships and technologies can help? By implementing these strategies, manufacturers can achieve efficiency and environmental responsibility.