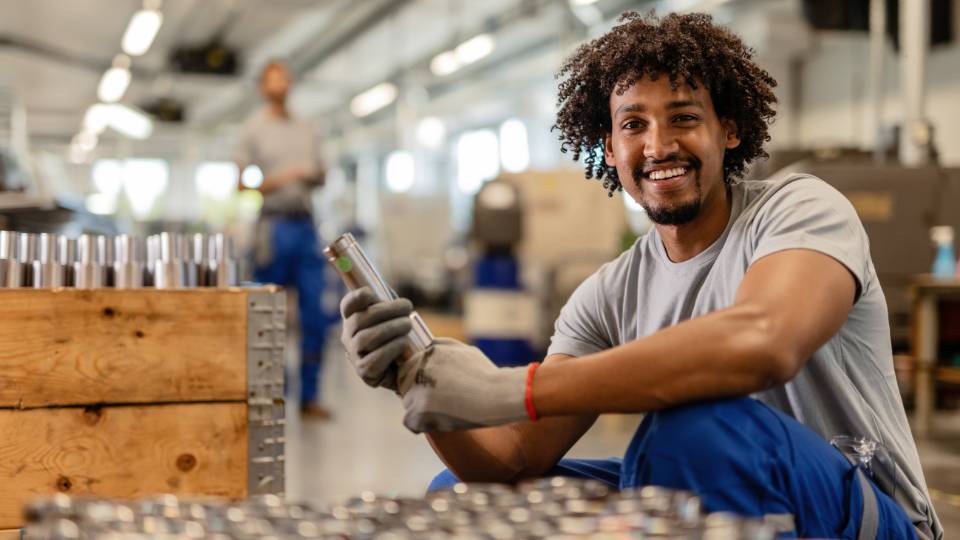
Manufacturing is one of the biggest contributors to waste outside of the construction & demolition industry.
That’s why establishing processes which maximise recycling potential while preventing cross-contamination wastage is crucial.
More than two-thirds of manufacturing waste originates from biological sources, such as sludge from wastewater and inedible food waste.
In cases where this waste is inevitable, we aim to derive value from these streams by exploring reuse opportunities, such as repurposing as animal feed, or recycling and converting them into new products, such as capturing biogas through anaerobic digestion or composting for agricultural use.
Table of Contents:
- What is manufacturing waste?
- Production waste from QA testing
- Manufacturing Waste – The 9 types
- What are the advantages of reducing manufacturing waste?
- 10 Strategies to Reduce Production Waste
- Conclusion
What is manufacturing waste?
Manufacturing waste refers to the materials left over during the production process of new products. Other names for this type of waste include factory waste, industrial waste, construction waste, and production waste.
The most common type of waste produced during product manufacturing includes scrap metal, concrete, plaster, food products, medicines and chemicals.
Production waste typically occurs as part of the manufacturing process. Some sites are better than others at designing the most efficient process possible for making building products with minimal loss of material.
Establishing an efficient process can eliminate wasted resources in terms of material & revenue. Anyone who has worked in the manufacturing industry will understand that the product design phase is a walk in the park when compared to the production process design.
You may have the best product in the world, but if you can’t efficiently put it together then the end result is not going to be market viable.
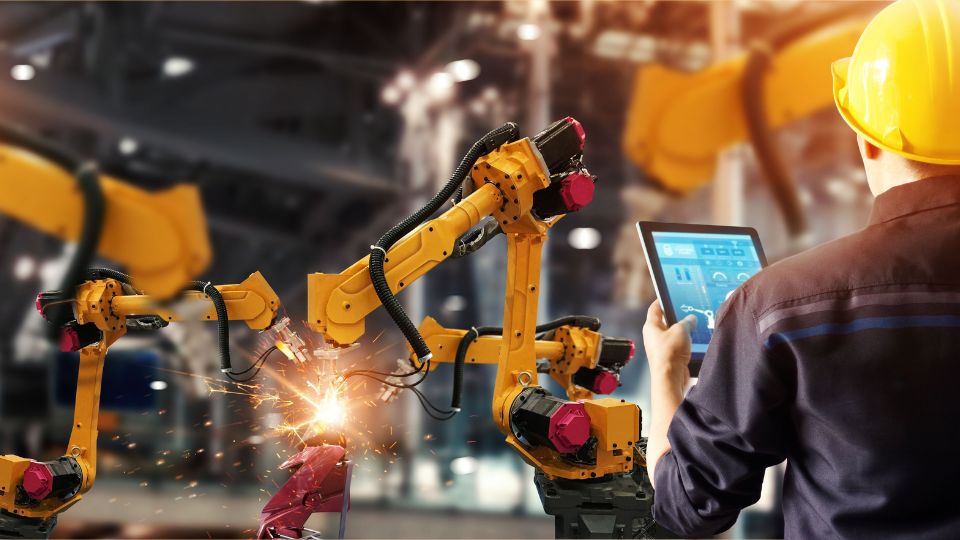
Production waste from QA testing
Loss of batches due to quality assurance (QA) testing can occur in various industries, including pharmaceuticals, food production, technology, and automotive.
Here are examples of how it can happen in each industry:
Pharmaceutical Industry:
- Failed Stability Testing: Pharmaceutical products undergo stability testing to ensure they maintain their quality throughout their shelf life. If a batch fails stability testing, it may need to be discarded to prevent potential harm to consumers.
- Contamination: Contamination during manufacturing or packaging processes can lead to batches being rejected during QA testing. Contaminants may include impurities, microorganisms, or foreign particles.
- Incorrect Labeling: Batches may be rejected if they do not meet labelling requirements, such as incorrect dosage information, expiration dates, or missing warnings.
Food Production:
- Microbiological Contamination: Food products must undergo microbiological testing to ensure they are free from harmful bacteria such as Salmonella or E. coli. If a batch tests positive for contamination, it must be discarded to prevent foodborne illness.
- Chemical Contamination: Similar to pharmaceuticals, food products can be rejected if they contain harmful chemical contaminants, such as pesticides, heavy metals, or additives exceeding legal limits.
- Allergen Cross-Contamination: If a batch is found to contain undeclared allergens due to cross-contamination during manufacturing, it may need to be recalled or discarded to prevent allergic reactions in consumers.
Technology:
- Functionality Testing: Electronic devices undergo rigorous testing to ensure they function properly and meet performance standards. If a batch of devices fails functionality testing due to defects or malfunctions, it may be rejected.
- Quality Control Defects: Components or materials used in manufacturing technology products are often subject to quality control testing. If a batch of components fails to meet specifications, it may result in the rejection of the entire batch.
- Safety Testing: Devices such as smartphones, laptops, or appliances must meet safety standards to prevent hazards such as electrical fires or radiation exposure. If a batch fails safety testing, it may be recalled or scrapped.
Automotive:
- Durability Testing: Automotive parts and vehicles undergo durability testing to ensure they can withstand various environmental conditions and usage scenarios. If a batch fails durability testing, it may be rejected due to concerns about reliability and safety.
- Quality Control Checks: Components used in automotive manufacturing are subject to quality control checks to ensure they meet specifications. If a batch of components fails to meet quality standards, it may result in the rejection of the entire batch, impacting assembly lines and production schedules.
- Safety Standards: Vehicles must meet safety standards to protect occupants in the event of accidents. If a batch of vehicles fails safety testing or does not meet regulatory requirements, it may be recalled or scrapped to prevent potential injuries or fatalities.
In all of these industries, the loss of batches due to QA testing underscores the importance of maintaining high-quality standards to ensure consumer safety and product efficacy.
While it may result in financial losses and production delays, it ultimately helps uphold the integrity and reputation of the brand or company.
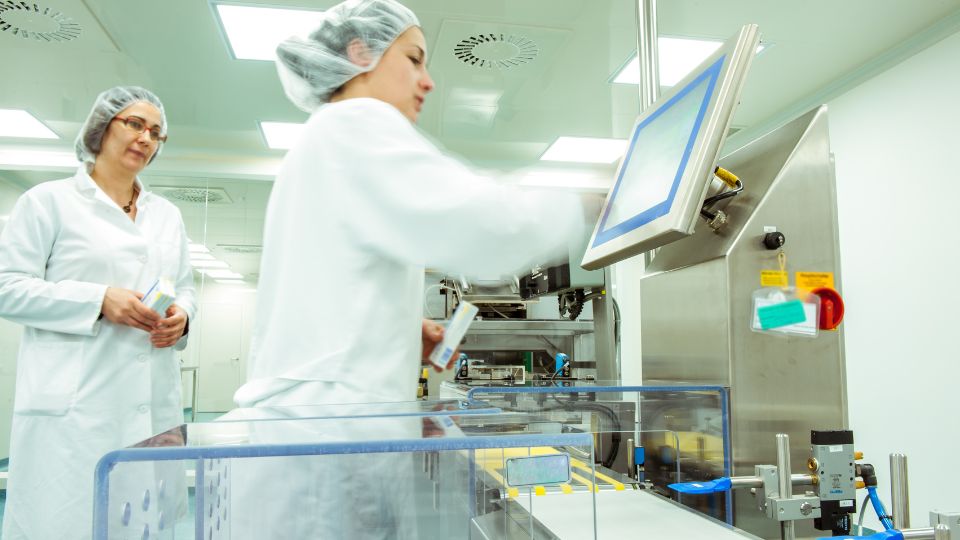
Manufacturing Waste – The 9 types
There are various causes of waste in manufacturing, which can be classified into 9 types:
- Defects – Defective products result in wasted time and materials that could have been used to create usable items. A manufacturing data collection system can help identify the root cause of defects so that the issue can be rectified at the source.
- Excess Processing – Poor product design, inefficient communication, and human error can all lead to unnecessary steps during the production process. This over-processing leads to avoidable waste.
- Overproduction – Producing extra product components before they are needed is a waste of time and resources, and an example of waste in manufacturing operations.
- Waiting – Downtime, such as when a machine awaits maintenance or when waiting for raw materials to arrive, is a form of lean manufacturing waste. It may result from poor planning or scheduling.
- Excess Inventory – Having more inventory than necessary to fulfil existing orders could result in high storage costs and other problems. It suggests a need to review manufacturing waste management procedures.
- Transportation – Enhancing the efficiency of transporting materials from one location to another can significantly contribute to reducing manufacturing waste in UK factories.
- Motion – Any unnecessary motion, including movement of machine parts during operation and employees manually performing tasks that could be automated, is considered non-value-add and adds to waste.
- Underutilised Talent – Failing to utilise employees’ talents to their full potential results in significant waste in operations, as companies miss out on potential ideas, skills, and improvements.
- Unused Energy – Wastage of energy resources, such as electricity, gas, or water, due to inefficient processes or equipment, contributes to manufacturing waste and impacts both costs and environmental sustainability.
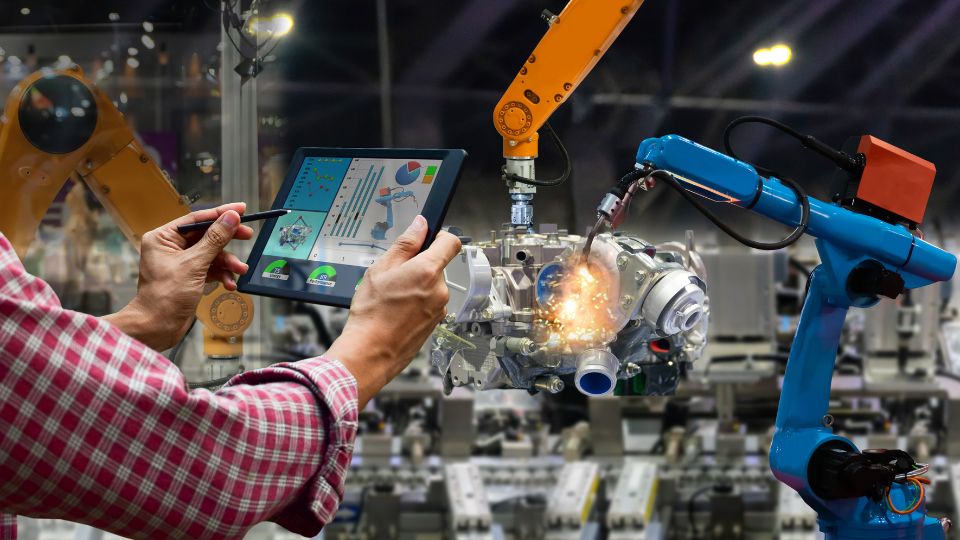
What are the advantages of reducing manufacturing waste?
Decreasing waste in manufacturing not only offers benefits to individual businesses but also has positive effects on the global economy and environment.
This reduction leads to reduced expenses, decreased overtime requirements, and enhanced product quality for manufacturers.
Furthermore, it aids in reducing carbon footprints and mitigating pollution, thus contributing to a healthier planet for all.
Many by-product are able to be recycled. A good example is the use of food wastage being converted into whey to be sold as suplements in the sports industry.
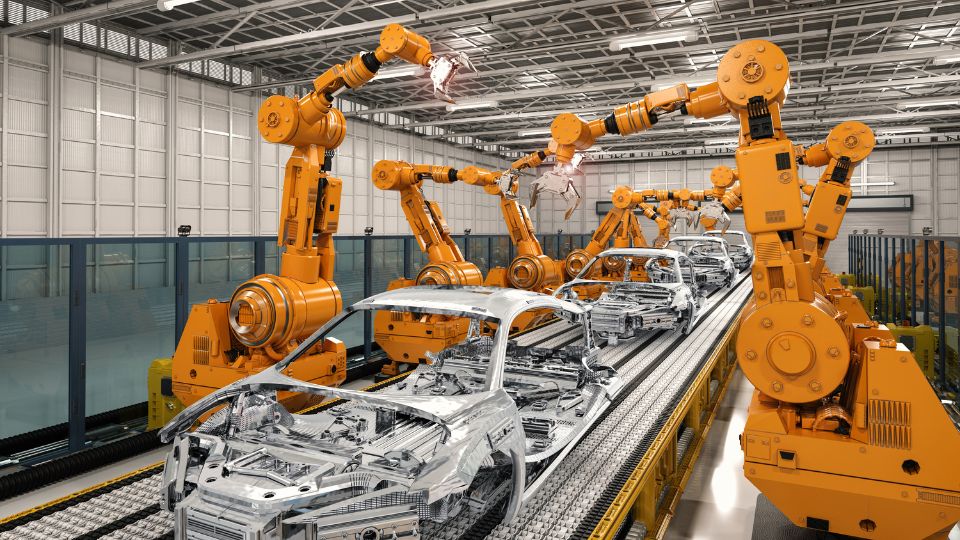
10 Strategies to Reduce Production Waste
Here are ten tips to help you minimise waste in manufacturing processes:
1. Establish a production waste management goal:
- Define a clear objective for reducing waste, such as aiming to cut waste by 25% in the next quarter.
Tracking progress against this goal is vital for measuring success and guiding improvement efforts.
In the UK, manufacturing waste significantly impacts the environment, with nearly 8.9 million tonnes generated annually.
2. Minimise overstocking and overproduction of waste:
- Implement a pull-based production system to avoid excess resources and manufacture items only when needed. This lean approach enhances efficiency and reduces waste.
3. Manage inventory effectively:
- Maintain optimal stock levels to prevent waste and implement robust inventory tracking systems to ensure timely product usage and avoid expired stock.
4. Implement preventive maintenance schedules:
- Regular equipment maintenance prevents unexpected breakdowns, minimising production delays and repair costs.
5. Optimise communication between staff:
- Ensure efficient communication among staff to prevent errors and delays, streamlining workflows and reducing production waste.
6. Reduce packaging waste:
- Review packaging practices to minimise waste, such as using recyclable materials or reducing packaging size, yielding significant environmental and financial benefits.
7. Conduct professional waste audits:
- Analyse waste streams to identify opportunities for production waste reduction, considering hiring external auditors to achieve green certification and enhance sustainability practices.
8. Invest in circular economy processes:
- Promote eco-friendly practices emphasising reuse, repair, refurbishing, and recycling, aiming for zero waste production processes to align with circular economy principles.
9. Explore creative solutions for waste:
- Identify valuable byproducts and explore opportunities for repurposing. For example, the transformation of whey from food production waste to a lucrative industry in the sports supplement market demonstrates the potential for innovative waste utilisation.
10. Implement energy efficiency measures:
- Reduce energy consumption through efficient equipment usage and renewable energy sources, contributing to cost savings and environmental sustainability while minimising waste.
Conclusion
Reducing manufacturing waste is not only an ethical imperative but also a strategic business decision. By implementing the ten strategies outlined in this article, companies can minimise their environmental impact, enhance operational efficiency, and improve their bottom line.
From setting clear waste management goals to exploring innovative solutions for waste repurposing, each step plays a crucial role in achieving a more sustainable and responsible manufacturing process.
By adopting a holistic approach to waste reduction, companies can contribute to building a more sustainable future while also enhancing their competitiveness in the market.